반도체 엔지니어를 위한 CVD 공정 완벽 가이드
안녕하세요, 반도체 공정에 관심 있는 엔지니어 여러분! 오늘은 반도체 제조의 핵심 기술 중 하나인 CVD(Chemical Vapor Deposition, 화학기상증착) 공정에 대해 자세히 알아보겠습니다.
목차
1. CVD란 무엇인가?
CVD는 기체 상태의 화학 물질(전구체)을 이용해 고체 물질을 기판 위에 증착하는 기술입니다. 반도체 제조에서는 절연막, 전도막, 반도체막 등 다양한 박막을 형성하는 데 사용됩니다.
1.1 CVD의 역사
- 1880년대: 백열전구 필라멘트 제조에 처음 사용
- 1960년대: 반도체 산업에 본격적으로 도입
- 1980년대: PECVD 기술 개발로 저온 공정 가능해짐
- 2000년대 이후: ALD 기술의 상용화로 나노 스케일 제어 가능
1.2 CVD vs PVD
CVD와 PVD(Physical Vapor Deposition)는 모두 박막 증착 기술이지만, 다음과 같은 차이가 있습니다:
특성 | CVD | PVD |
---|---|---|
증착 메커니즘 | 화학 반응 | 물리적 증발/스퍼터링 |
작동 압력 | 대기압~고진공 | 고진공 |
증착 온도 | 일반적으로 높음 | 상대적으로 낮음 |
단차피복성 | 우수 | 제한적 |
증착 속도 | 중간~빠름 | 느림~중간 |
불순물 제어 | 어려움 | 상대적으로 쉬움 |
2. CVD의 기본 원리
CVD 공정은 다음과 같은 단계로 이루어집니다:
- 전구체 가스 주입
- 가스 확산
- 표면 흡착
- 화학 반응
- 부산물 제거
2.1 CVD 반응 동역학
CVD 공정의 반응 속도는 다음 두 가지 요인에 의해 결정됩니다:
- 표면 반응 율속 단계: 낮은 온도에서 주로 발생, 아레니우스 방정식을 따름
R = A * exp(-Ea/RT) R: 반응 속도, A: 빈도 인자, Ea: 활성화 에너지, R: 기체 상수, T: 절대 온도
- 물질 전달 율속 단계: 높은 온도에서 주로 발생, 확산에 의해 제한됨
R = hG * (Cg - Cs) R: 반응 속도, hG: 물질 전달 계수, Cg: 가스 농도, Cs: 표면 농도
3. CVD의 장점
- 균일한 박막 형성
- 높은 순도
- 에피택시얼 성장 가능
- 다양한 물질 증착
- 우수한 단차피복성
- 대면적 증착 가능
4. CVD의 종류
CVD 공정은 크게 다음과 같이 나눌 수 있습니다:
종류 | 특징 | 장점 | 단점 | 주요 응용 분야 |
---|---|---|---|---|
APCVD | 대기압에서 진행 | 간단한 장비, 높은 증착 속도 | 균일도 저하, 오염 가능성 | 저가 제품의 산화막 증착 |
LPCVD | 저압에서 진행 | 우수한 균일도, 다수 웨이퍼 처리 | 낮은 증착 속도, 고온 필요 | 다결정 실리콘, 질화막 증착 |
PECVD | 플라즈마 이용 | 저온 공정, 다양한 물질 증착 | 플라즈마 손상 가능성 | 패시베이션막, 층간절연막 증착 |
HDPCVD | 고밀도 플라즈마 이용 | 우수한 갭필 특성 | 장비 복잡성, 높은 비용 | STI 갭필, 금속간 절연막 |
ALD | 원자층 단위 증착 | 정밀한 두께 제어 | 매우 낮은 증착 속도 | 고유전율 게이트, 배리어 메탈 |
MOCVD | 유기금속 전구체 사용 | 다양한 화합물 반도체 증착 | 전구체 비용 높음 | III-V 족 반도체, LED 제조 |
4.1 PECVD 세부 설명
PECVD는 플라즈마를 이용해 저온에서 CVD 공정을 수행합니다. 주요 특징은 다음과 같습니다:
- 작동 온도: 200-400°C
- 압력 범위: 0.1-10 Torr
- 플라즈마 생성: RF (13.56 MHz) 또는 마이크로웨이브 (2.45 GHz) 사용
- 장점: 저온 공정, 응력 제어 가능, 수소 함량 조절 가능
- 단점: 이온 충돌에 의한 기판 손상 가능성
PECVD 공정에서 중요한 파라미터:
- RF 파워: 플라즈마 밀도와 이온 에너지 결정
- 압력: 평균 자유 행로와 라디칼 수명에 영향
- 가스 조성: 박막의 화학적 조성 결정
- 기판 온도: 표면 반응과 수소 함량에 영향
5. CVD 공정의 핵심 파라미터
CVD 공정에서 가장 중요한 것은 파라미터 제어입니다. 주요 파라미터와 그 영향을 표로 정리했습니다.
파라미터 | 영향 | 일반적인 범위 | 주의사항 |
---|---|---|---|
온도 | 반응 속도, 막질 | 200-1100°C | 기판 손상 주의 |
압력 | 균일도, 증착 속도 | 0.1-760 Torr | 저압: 균일도↑, 속도↓ |
가스 유량 | 균일도, 증착 속도 | 10-1000 sccm | 과다 유량 시 난류 발생 |
전구체 농도 | 증착 속도, 막질 | 0.1-10% | 고농도 시 가스상 반응 주의 |
RF 파워 (PECVD) | 플라즈마 밀도 | 100-1000W | 과다 파워 시 기판 손상 |
5.1 온도의 영향
온도는 CVD 공정에서 가장 중요한 파라미터 중 하나입니다. 온도에 따른 영향:
- 저온 (< 500°C):
- 표면 반응 율속
- 느린 증착 속도
- 비정질 또는 다결정 구조
- 높은 불순물 함량
- 고온 (> 800°C):
- 물질 전달 율속
- 빠른 증착 속도
- 결정성 향상
- 열응력 발생 가능성
5.2 압력의 영향
압력은 반응 기체의 평균 자유 행로와 체류 시간에 영향을 줍니다:
- 고압 (> 100 Torr):
- 짧은 평균 자유 행로
- 가스상 반응 증가
- 높은 증착 속도
- 불균일한 막질
- 저압 (< 1 Torr):
- 긴 평균 자유 행로
- 표면 반응 우세
- 우수한 단차피복성
- 낮은 증착 속도
6. CVD 공정 최적화 팁
- 온도 조절:
- 목표: 원하는 박막 특성 획득 + 기판 손상 최소화
- 방법: 온도를 50°C 단위로 변화시키며 최적점 탐색
- 예: SiO2 증착 시 700°C에서 시작해 650°C, 750°C 테스트
- 압력 관리:
- 저압: 균일한 막질, 느린 증착
- 고압: 빠른 증착, 균일도 저하
- 방법: 로그 스케일로 압력 변화 (예: 0.1, 1, 10 Torr)
- 가스 유량 최적화:
- 과다: 난류 발생, 전구체 낭비
- 과소: 불균일한 증착, 느린 속도
- 방법: 총 유량 고정, 개별 가스 비율 조절
- 전구체 선택:
- 목표 박막 특성에 맞는 전구체 선정 중요
- 예: SiO2 증착 시 TEOS vs. SiH4 비교
- TEOS: 우수한 단차피복성, 저온 공정
- SiH4: 빠른 증착 속도, 높은 순도
- 실험 계획법 (DOE) 활용:
- 완전 요인 설계: 모든 인자 조합 테스트
- 부분 요인 설계: 주요 인자만 선별하여 테스트
- 반응 표면 분석: 최적점 예측 및 검증
7. 실제 공정 예시: 실리콘 산화막(SiO2) 증착
실리콘 산화막은 반도체에서 가장 흔히 사용되는 절연막입니다. TEOS(Tetraethyl orthosilicate)를 이용한 CVD 공정으로 증착할 수 있습니다.
반응식: Si(OC2H5)4 + 2H2O → SiO2 + 4C2H5OH
온도: 650-750°C
압력: 1-2 Torr TEOS
유량: 30-50 sccm
산소 유량: 40-60 sccm
이 조건에서 약 10-15 nm/min의 속도로 균일한 SiO2 막을 얻을 수 있습니다.
7.1 TEOS vs. Silane 비교
특성 | TEOS | Silane (SiH4) |
---|---|---|
안전성 | 높음 (액체) | 낮음 (가연성 가스) |
증착 온도 | 600-750°C | 400-900°C |
증착 속도 | 10-20 nm/min | 20-100 nm/min |
단차피복성 | 우수 | 보통 |
막질 | 치밀, 저응력 | 고밀도, 고응력 |
수분 흡수 | 낮음 | 높음 |
8. 최신 CVD 기술 동향
- 원자층 증착(ALD) 기술의 발전
- 초박막 증착에 유리
- 높은 종횡비 구조에서 우수한 단차피복성
- 응용 분야: 고유전율 게이트 절연막, 금속 배리어, DRAM 캐패시터
- 선택적 증착 기술
- 특정 영역에만 선택적으로 박막 형성
- 패터닝 공정 간소화 가능
- 예: 텅스텐 플러그 형성 시 선택적 CVD
- 저온 CVD 공정 개발
- 열에 민감한 차세대 소자 제작에 필수
- 플라즈마 활용, 새로운 전구체 개발 등
- 응용: 플렉시블 디스플레이, 3D 적층 구조
- 3D 구조에서의 CVD 적용
- 고종횡비 구조에서의 균일한 박막 형성
- 나노 구조에서의 CVD 기술 발전
- 예: FinFET, 3D NAND 플래시 메모리
- 환경 친화적 CVD 기술
- 저독성 전구체 사용
- 부산물 최소화 및 재활용 기술 개발
- 예: 불소계 가스 대체, 암모니아 대신 질소 사용
9. CVD 공정의 문제점 및 해결 방안
CVD 공정은 많은 장점에도 불구하고 몇 가지 중요한 문제점을 가지고 있습니다. 이러한 문제점들과 그에 대한 해결 방안을 살펴보겠습니다.
9.1 주요 문제점
문제점 | 설명 | 해결 방안 |
---|---|---|
높은 작동 온도 | 기판의 열 불안정성 및 에너지 소비 증가 | 저온 CVD 기술 개발, 플라즈마 강화 CVD 사용 |
독성 및 위험 전구체 | 안전 위험 및 환경 문제 발생 | 안전한 대체 전구체 개발, 엄격한 안전 프로토콜 적용 |
균일성 문제 | 대면적 기판에서의 불균일한 증착 | 가스 흐름 최적화, 다중 영역 히터 사용 |
오염 및 불순물 | 박막 품질 저하 | 고순도 전구체 사용, 챔버 청결도 향상 |
9.2 세부 문제점 및 해결 방안
- 열악한 필름 품질
- 문제: 부정확한 온도, 반응물 유속, 기판 준비 등으로 인한 품질 저하
- 해결: 온도와 유속의 정밀한 제어, 기판 표면 처리 개선
- 균일성 문제
- 문제: 부적절한 가스 흐름 패턴 또는 기판 회전으로 인한 불균일한 증착
- 해결: 가스 흐름 패턴 최적화, 기판 회전 속도 조절
- 진공 펌프 고장
- 문제: 공정 중단 및 생산성 저하
- 해결: 정기적인 유지보수, 백업 펌프 시스템 구축
- 현장 측정의 어려움
- 문제: 실시간 공정 모니터링의 한계
- 해결: 첨단 in-situ 모니터링 기술 도입 (예: 광학적 방법, 플라즈마 발광 분석)
9.3 개선을 위한 전략
- 공정 파라미터의 지속적인 최적화
- 첨단 모니터링 및 제어 시스템 도입
- 정기적인 장비 유지보수 및 청소
- 환경 친화적이고 안전한 전구체 개발
- 시뮬레이션 기술을 활용한 공정 예측 및 최적화
이러한 문제점들을 해결하고 개선 전략을 적용함으로써 CVD 공정의 효율성과 신뢰성을 크게 향상시킬 수 있습니다. 지속적인 연구 개발을 통해 CVD 기술은 계속해서 발전하고 있으며, 반도체 및 다양한 산업 분야에서 중요한 역할을 담당할 것입니다.
10. 마치며
CVD 공정은 복잡하지만, 파라미터를 잘 제어하면 원하는 특성의 박막을 정확하게 만들 수 있습니다. 여러분의 공정에서 어떤 파라미터가 가장 중요한지 파악하고, 그에 맞춰 최적화해보세요.
이 글에서 다룬 내용은 CVD 공정의 기초부터 최신 동향까지 폭넓게 다루고 있습니다. 하지만 반도체 기술은 빠르게 발전하고 있으므로, 지속적인 학습과 실험이 필요합니다. 여러분의 경험과 이 지식을 바탕으로 더 나은 반도체 제조 공정을 개발하시기 바랍니다.
다음에는 CVD의 사촌뻘 되는 ALD 공정에 대해 자세히 알아보도록 하겠습니다.
끝까지 읽어주셔서 감사합니다.
공감과 구독, 그리고 댓글은
저의 블로그 활동에
큰 원동력이 됩니다.
오늘도 좋은 하루 보내세요♥
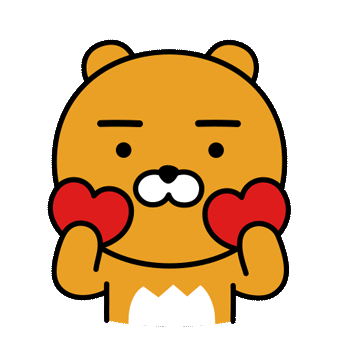
'유용한 스토리' 카테고리의 다른 글
★일본약 이제 국내반입금지?? 대체가능한 국산약 알려드림!! (0) | 2025.05.07 |
---|---|
30~40대가 인생에서 가장 중요한 이유 (0) | 2025.03.13 |
무협소설의 대가, 김용의 작품 소개 (1) | 2025.03.03 |
S&P500 패시브 투자 가이드 (0) | 2025.02.14 |
트럼프 대통령의 주요 행정명령과 영향 (0) | 2025.02.13 |